MEDICAL TECHNOLOGY
Hearing is of paramount importance for human beings, especially speech comprehension as part of interpersonal communication. If congenital or acquired hearing loss can no longer be corrected using hearing aids - technically speaking, a sound amplifier - there is another possibility: a so-called cochlear implant (CI), which stimulates the intact auditory nerve with the help of electrodes implanted in the cochlea. In addition to the transmitting (external) and receiving (internal) coils, the system also includes an audio processor with microphone that digitises the acoustic signals received before they are transmitted into the ear and cause corresponding stimulation of the auditory nerve. This speech reception, however, is not identical to natural hearing ability - listening comprehension must be practically reacquired through intensive training, which is roughly comparable to learning a foreign language.
Whereas the power to the implanted components is supplied via electromagnetic induction, the external speech processor is powered by a rechargeable battery. These two assemblies are normally worn behind the ear and are connected to the application described here using INGUN spring-loaded test probes (GKS): So-called short-stroke GKS are very compact and ensure the electrical transfer (40 mA at 6 V) from the battery to the audio processor as well as the quick exchange of the assemblies.
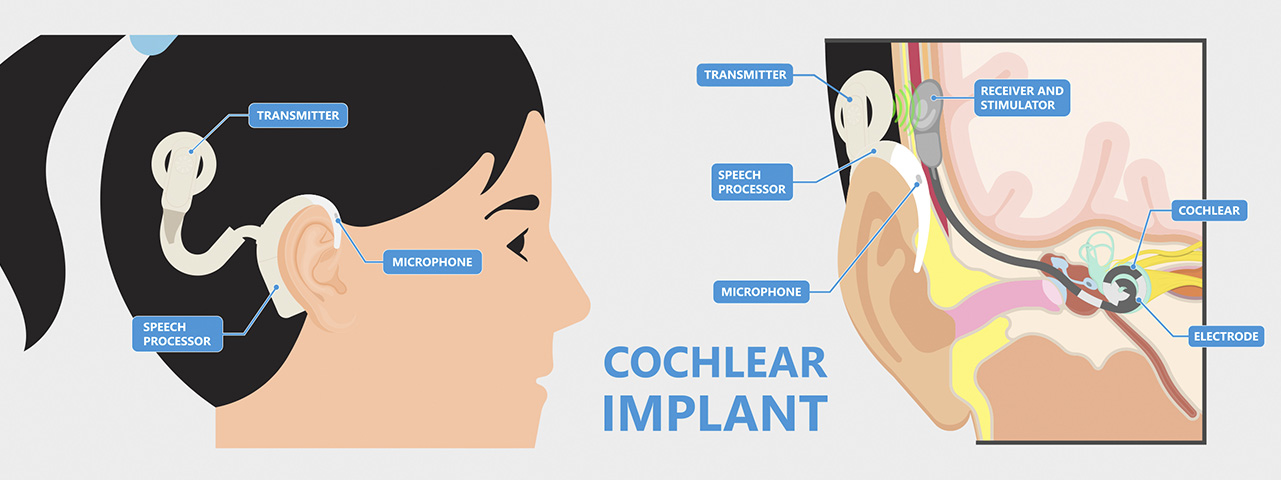
Although the test probes have an effective layer of plating and had already been tested with artificial welding, in practice, the requirements for corrosion resistance in this application proved to be exceptionally demanding. The combination of various metals, sweat, as well as electrolytes emitted by the body together with electric current flow results in a galvanic element that leads to increased electrochemical corrosion – ultimately resulting in loss of function: The probe’s plunger jams as soon as the installed spring is subject to excessive contamination.The analysis of the impurities revealed sodium, chlorine, carbon and oxygen originating from electrolytes emitted from the body in addition to the individual metal components such as tin, zinc, copper, gold and nickel.
In response to this challenge, INGUN carried out an extensive corrosion test in consultation with the customer, a CI manufacturer, and in cooperation with the University of Applied Sciences in Constance. The test was performed in accordance with DIN 50018 using an additional chloride load. The main aim was to determine how solder and flux influence the extent of corrosion, and to find combinations that are less susceptible to corrosion and can ensure a longer service life.
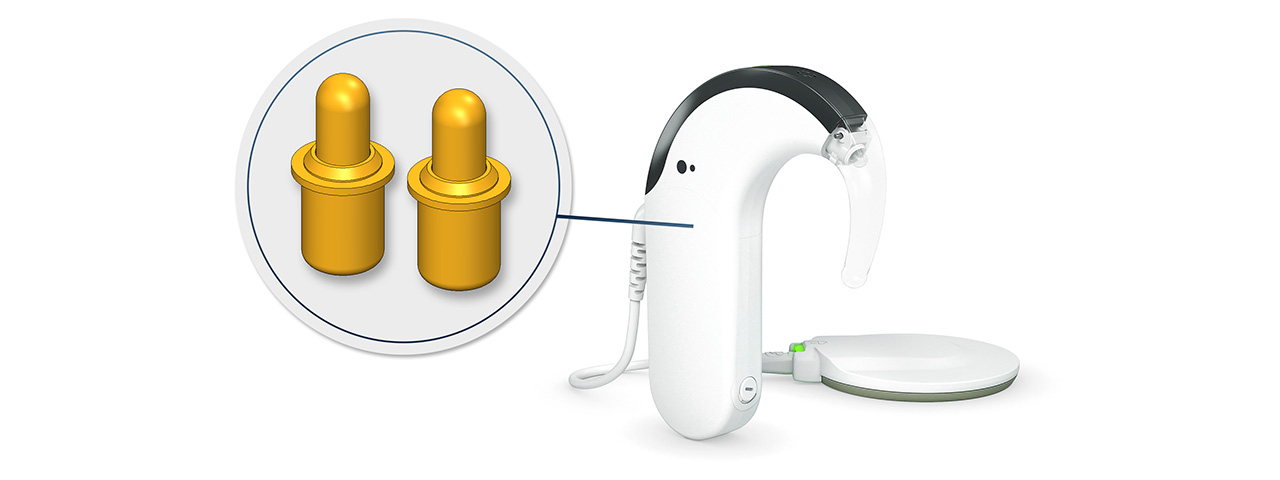
Peter Breul, Test Probe Project Administrator (Design Projects) at INGUN, explains why the application is a challenging environment for INGUN probes: "We are dealing with a chemical complexity that should not be underestimated: Our test probes are lubricated during production to ensure optimal mechanical function. When installing the probes, various solders, and a suitable flux are used to achieve solderability. Here it is important to achieve an optimum balance between the aggressiveness of the flux – which chemically cleans or removes the protective layer on the PCB or components to ensure effect soldering - and sufficient corrosion protection. Additional alloys are also created, especially at the edge of components, such as the solder joint and vias, due to the solder fusing with the surface material."
In the corrosion test, the four groups or four different probe versions (a sample of 16 probes) showed some very different results, from heavily corroded to only superficially contaminated (and almost "as good as new" after cleaning in an ultrasonic bath). Further steps finally showed that the use of a silver solder in combination with a suitable flux significantly reduces corrosion. In addition, a stainless steel spring in the test probe makes a significant contribution to maintaining the function over a longer period of time. "A further increase in service life could be achieved by optimising the plating material, but this was not considered further by the customer," Peter Breul continues.
After using the modified test probes with optimised plating, probe functionality improved, and surfaces withstood the highly corrosive environment for longer.Corrosion tests are, therefore, an effective means of obtaining reliable information about the performance of charging and transfer probes under challenging applications or cleaning procedures. This goes beyond medical technology and essentially concerns the entire gadgets and wearables sector. Besides corrosion tests in the narrower sense, other procedures are performed in other industries, such as salt spray or vibration tests. INGUN carries out these types of ageing tests in consultation with customers, if required, in order to optimise the performance and service life of GKS and other components.