BATTERY CELL FORMATION
Formation is the decisive step in the third and final phase of manufacturing lithium-ion batteries: once all components have been manufactured, assembled and packaged, the battery is charged and discharged in a controlled manner for the first time. As the currents gradually increase, a boundary layer forms between the anode and the electrolyte, known as the solid electrolyte interphase layer, or SEI layer for short.
This process can take up to 24 hours and is crucial for both the electrochemical quality and the performance of the battery. Cell manufacturers therefore invest considerable resources in optimising the formation process - especially for large automotive batteries that require high currents.
Energy-efficient contacting for high currents
The choice of contacting solutions plays a key role in power consumption and temperature development in the formation process. The greatest loss factor is the contact resistance between the contact element and the battery terminals. The aluminium alloys of the battery poles tend to form an oxide layer that impedes the flow of electrons and generates additional heat - both of which slow down the formation process. In order to shorten the formation time and reduce energy consumption, the contact resistance should be kept as low as possible.
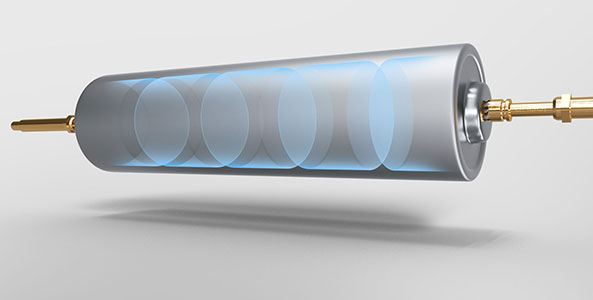
Lower resistance, reduced heat loss
INGUN offers innovative contacting solutions that minimise contact resistance thanks to specific tip shapes and high contact forces, enabling higher currents and faster charging and discharging cycles. This speeds up the moulding process and reduces operating costs.
The BCP (Battery Contact Probe) and BCC (Battery Contact Clamp) series offer optimum conditions for efficient and energy-saving forming.
Key features include:
- High-quality alloy: A specialised coating prevents tarnishing and ensures long-lasting, reliable connections.
- Non-moving cable: Direct mounting in busbars eliminates the need for complex cable assembly - for maximum stability and simplified installation.
- Unique tip style: The probes penetrate aluminium oxide layers effortlessly, ensuring low-loss, reliable contacting.
- Flexible cooling options: Both active and passive cooling options are available, optimally adapted to the requirements of the formation process
Scaling and flexible assembly
The savings potential increases further if several probes are connected simultaneously, for example to contact large batteries at module and pack level. We have developed the multi-head connector for this purpose: With this technology, a configuration of various probes with different tip styles, spring forces, and coatings can be combined. If required, voltage and temperature measurements, as well as active cooling, can also be integrated to further optimise the formation process.
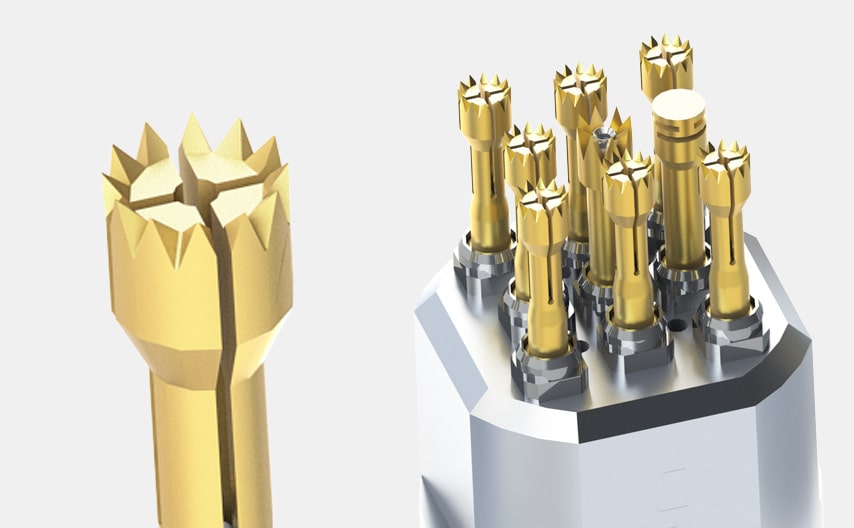