Especially in the testing of electronic devices, unavoidable positioning tolerances often occur. Board-to-board (B2B) connectors and numerous automotive connectors in particular are subject to significant position and angle deviations as a result of the soldering process on the printed circuit board (PCB). Suitable floating mechanisms are used here to compensate for these inaccuracies and ensure reliable, replicable contacting.
Reliable tolerance compensation in connector testing
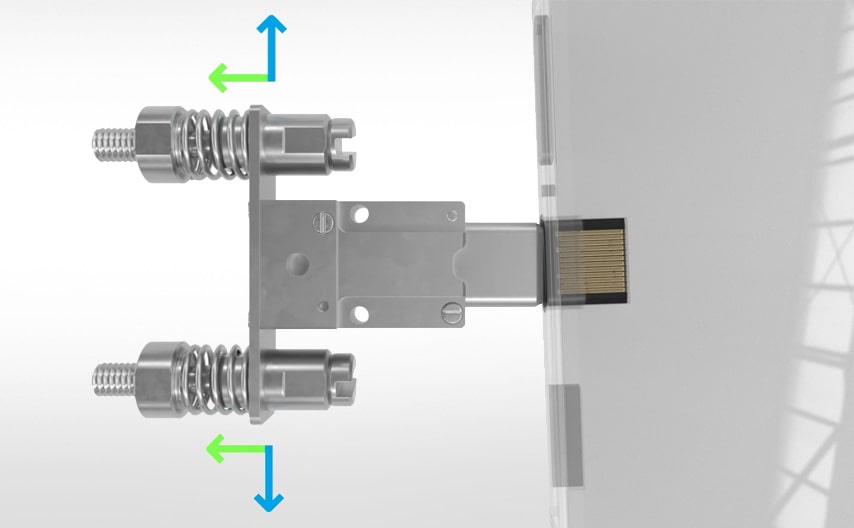
To make test sequences more efficient, floating mechanisms can be integrated directly into test plugs. These integrated solutions vary in design, spring force, and range of motion depending on the application.
Various floating mechanisms are available for a range of test solutions, each of which can compensate for specific positioning and angular errors (e.g. ±2.5°). To make it easier for you to choose, we provide a clear recommendation for each product that is precisely tailored to the requirements of the connector and test application. Our experts analyse the combination of the device to be tested (DUT) and contacting solution, then determine the optimum spring force. By doing so, we ensure that every component is tested reliably.
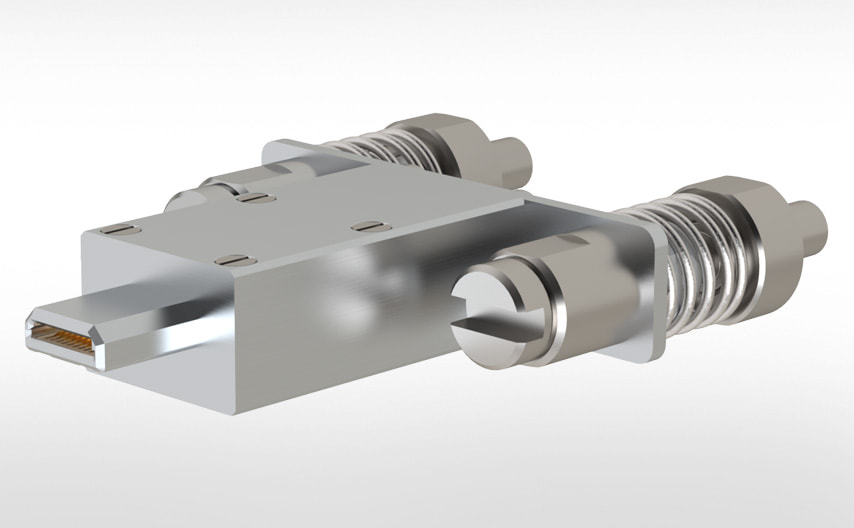
Practical example: Reliable contacting of automotive connectors
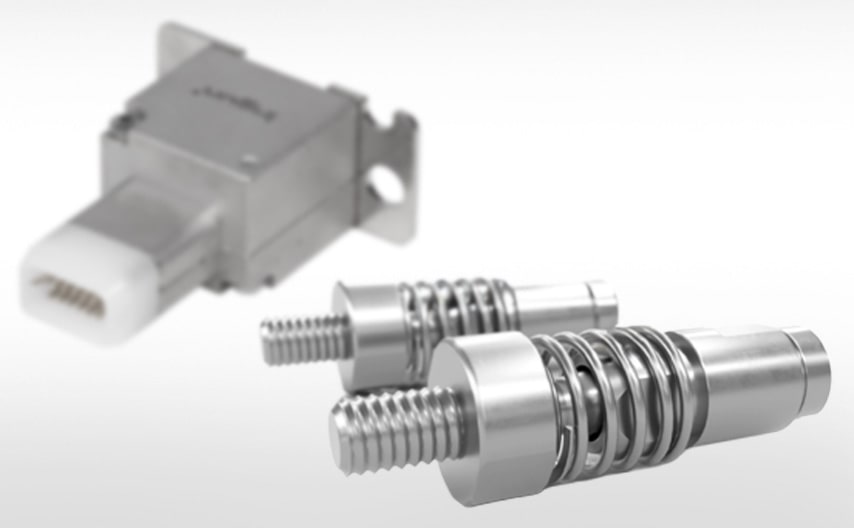
A typical example of the use of floating mechanisms is with automotive connectors such as the Molex HSAutoLink™ II. These connectors have been specially developed for high-speed data transmission in modern vehicle networks – such as infotainment or driver assistance systems. They are available in sealed and unsealed versions with 6 or 14 circuit options and support automotive media protocols such as, Ethernet, USB, and others.
These connectors in particular often have significant positioning and angular deviations after they are soldered onto printed circuit boards (PCBs). In order to be able to test automatically, reliably and consistently, float mechanisms are indispensable.
A typical test set-up with an integrated floating mechanism:
- The test plug uses the chamfered surface to ensure pre-centring which is dependent on the plastic housing of the connector.
- Thanks to the optionally available spring elements, the test plug then aligns itself with the DUT.
- This allows positional deviations of up to ±0.7 mm and angle tolerances of ±2 degrees to be reliably compensated.
- The optionally available set of two springs - 13 N per side - ensure a reliable, replicable contact force that is ideally suited to the DUT.
Multi-stage floating mechanisms for B2B connectors
Positional and angular errors also pose a challenge for automated testing in board-to-board connectors. Therefore, we offer test probes (e.g. HFS-511 and HFS-556) with multi-stage floating mechanism specially developed for first and second generation B2B connectors:
- Stage 1 – Initial alignment: The test probe is initially aligned with the housing of the B2B connector.
- Level 2 – Fine adjustment: Any angular and rotational errors are precisely compensated for upon approach.
- Level 3 – Reliable contacting: During the working stroke, the spring-loaded inner conductors and housing ensure optimum contact force without damaging the sensitive contact surfaces on the DUT. .
Got questions? Unsure which floating mechanism best suits your testing requirements?
Our Customer Service team is always there for you. Use the contact form below or simply pick up the phone:
+49 7531 8105 888