MEDIZINTECHNIK
Das Hören ist für den Menschen von eminenter Bedeutung, insbesondere das Sprachverstehen als Teil der Kommunikation untereinander. Wenn sich angeborene oder erworbene Defekte des Hörsinns nicht mehr mit einem Hörgerät – technisch gesehen einem Schallverstärker – korrigieren lassen, gibt es noch eine weitere Möglichkeit: Ein sogenanntes Cochlea-Implantat (CI) stimuliert den intakten Hörnerv mit Hilfe von Elektroden, die in die Hörschnecke (lat. Cochlea) implantiert werden. Zum Gesamtsystem gehört neben der Sende- (außen) und Empfangsspule (innen) auch ein Audioprozessor mit Mikrofon, der die empfangenen akustischen Signale digitalisiert, bevor sie ins Innere übertragen werden und entsprechende Stimulationen des Hörnervs hervorrufen. Die Sprachrezeption ist jedoch mit dem natürlichen Weg nicht identisch – das Hörverstehen muss durch intensives Training praktisch neu erworben werden, was in etwa mit dem Erlernen einer Fremdsprache vergleichbar ist.
Während die Stromversorgung der implantierten Komponenten über elektromagnetische Induktion erfolgt – innere und äußere Spule werden mit Magneten in Position zueinander gehalten – wird der externe Sprachprozessor mit einem Akku betrieben. Diese beiden Baugruppen werden normalerweise hinter dem Ohr getragen und sind im hier beschriebenen Anwendungsfall über gefederte Kontaktstifte (GKS) von INGUN verbunden. Diese sogenannten Kurzhub-GKS sind sehr kompakt ausgeführt und stellen die elektrische Übergabe (40 mA bei 6 V) vom Akku zum Audioprozessor sowie den schnellen Wechsel der Baugruppen sicher.
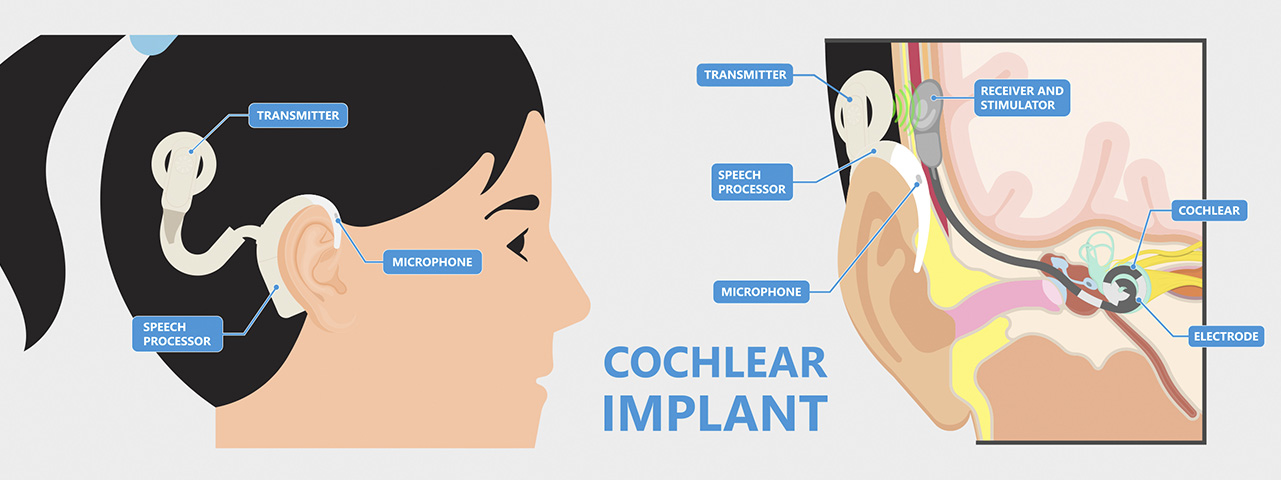
Obwohl die Kontaktstifte über eine entsprechende Veredelung verfügen und bereits zuvor mit künstlichem Schweiß getestet worden waren, stellte sich in der Praxis heraus, dass die Anforderungen an die Korrosionsbeständigkeit bei einer solchen Anwendung außergewöhnlich hoch sind. Die Kombination aus verschiedenen Metallen (Lot und Veredelung), Schweiß und Körperrückständen als Elektrolyt sowie elektrischem Stromfluss ergibt ein galvanisches Element, das zu verstärkter elektrochemischer Korrosion führt – bis hin zum Funktionsverlust: Die Kolben klemmen, sobald die verbaute Feder zu stark angegriffen ist. Bei der Analyse der Verunreinigungen zeigten sich neben den einzelnen Metallbestandteilen wie Zinn, Zink, Kupfer, Gold und Nickel auch Natrium, Chlor, Kohlenstoff und Sauerstoff, die von Körperrückständen herrühren.
Als Antwort auf diese Herausforderung führte INGUN in Absprache mit dem Kunden, einem CI-Hersteller, und in Zusammenarbeit mit der Fachhochschule Konstanz einen erweiterten Korrosionstest durch. Zum einen bestand das Ziel darin, das Ausmaß der Korrosion und ihre Ursachen möglichst genau zu ermitteln. Hierzu wurde ein Test nach DIN 50018 (Kondenswasser-Wechselklima mit schwefeldioxidhaltiger Atmosphäre) mit zusätzlicher Chlorid-Belastung durchgeführt. Zum anderen ging es vor allem darum, den Einfluss von Lot und Flussmittel auf das Ausmaß der Korrosion zu ermitteln sowie solche Kombinationen zu finden, die sich weniger anfällig zeigen und somit für eine längere Standzeit sorgen können.
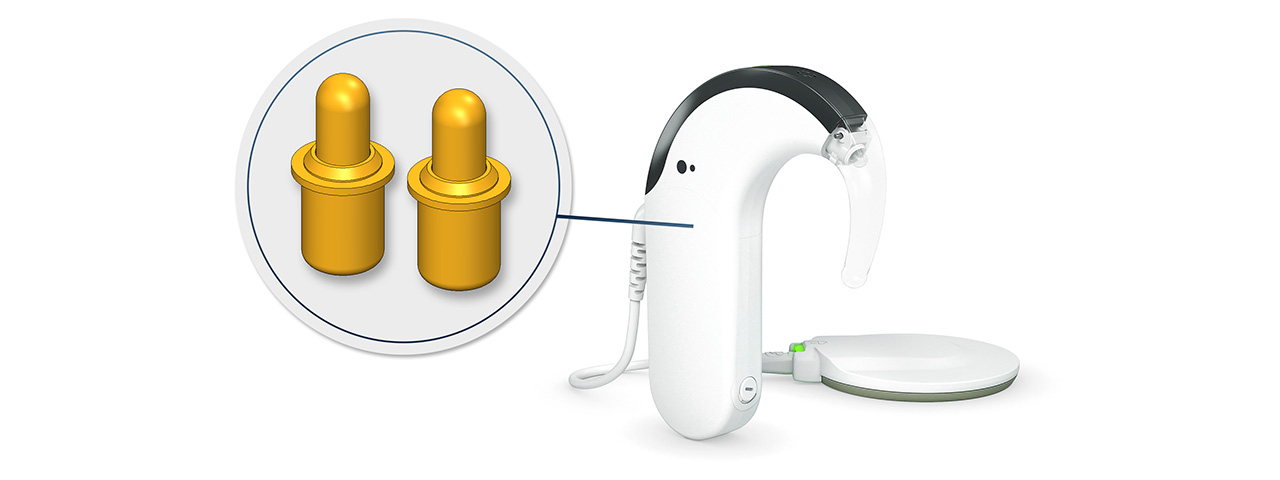
Peter Breul, Test Probe Project Administrator (Design Projects) bei INGUN, erläutert die Hintergründe: „Wir haben es hier mit einer nicht zu unterschätzenden chemischen Komplexität zu tun: Zunächst unterliegen unsere Kontaktstifte einer Dauerschmierung zur Sicherstellung der Kontaktierung. Dann werden beim Einbau verschiedene Lote sowie ein geeignetes Flussmittel eingesetzt, um die Lötfähigkeit zu erreichen. Hier gilt es, ein Optimum zwischen der Aggressivität für das Anätzen der Leiterplatte zur Herstellung eines elektrischen Kontakts sowie demgegenüber einem ausreichenden Korrosionsschutz zu erzielen. Besonders an den Randschichten wie der Lötstelle und dem Via kommt es zudem regelmäßig zu Legierungen, die nur schwer zu kontrollieren sind.“
Beim Korrosionstest zeigten die 16 verschiedenen Kontaktstifte in vier Gruppen teils sehr unterschiedliche Resultate, von stark angegriffen bis nur oberflächlich verunreinigt (und nach dem Ultraschallbad wieder fast „wie neu“). In weiteren Schritten ergab sich schließlich, dass die Verwendung eines Silberlots in Kombination mit einem geeigneten Flussmittel die Korrosion deutlich reduziert. Außerdem trägt eine Edelstahlfeder im Kontaktstift entscheidend zur Aufrechterhaltung der Funktion über einen längeren Zeitraum bei. „Eine weitere Erhöhung der Standzeit könnte über eine optimierte Veredelung erreicht werden, was jedoch von Kundenseite nicht weiter in Betracht gezogen wurde“, so Peter Breul weiter.
Nach dem Einsatz der entsprechend angepassten GKS gab es endkundenseitig keine frühzeitigen Ausfälle mehr – sowohl die Funktionalität als auch die Oberflächen hielten der stark korrosiven Umgebung über längere Zeit stand. Korrosionstests sind damit ein wirksames Mittel, um bei schwierigen Einsatz- oder Reinigungsbedingungen verlässliche Aussagen über die Leistungsfähigkeit von Lade- und Übergabestiften zu gewinnen. Dies geht auch über die Medizintechnik hinaus und betrifft im Prinzip den gesamten Bereich der Gadgets und Wearables. Neben Korrosionstests im engeren Sinne kommen in anderen Branchen weitere Verfahren vor, etwa Salzsprüh- oder Vibrationstests. INGUN führt in Absprache mit Kunden bei Bedarf solche Alterungstests durch, um Performance und Lebensdauer von GKS und weiteren Komponenten zu optimieren.