TECHNOLOGíA MÉDICA
La audición es de importancia capital para los seres humanos, en especial la comprensión del lenguaje como parte de la comunicación interpersonal. Cuando los defectos innatos o adquiridos del sentido del oído ya no pueden corregirse con un auxiliar auditivo –visto técnicamente, un amplificador de sonidos–, todavía existe otra posibilidad: El llamado implante de cóclea (IC) estimula al nervio auditivo intacto con ayuda de electrodos que se implantan en el caracol del oído (en latín, cochlea). Además de la bobina de envío (externa) y de recepción (interna), también forma parte del sistema completo un procesador de audio con micrófono que digitaliza las señales acústicas recibidas antes de que se transmitan al interior y produzcan los correspondientes estímulos del nervio auditivo. Sin embargo, la recepción del lenguaje no es idéntica a la forma natural: la comprensión auditiva prácticamente tiene que volver a obtenerse con un intenso entrenamiento, lo que puede compararse aproximadamente al aprendizaje de una lengua extranjera.
Mientras que el suministro de corriente de los componentes implantados se realiza a través de inducción electromagnética –la bobina interna y externa se mantienen en posición una respecto a la otra mediante imanes– el procesador de lenguaje externo se acciona con una batería. Estos dos grupos de componentes se llevan normalmente detrás de la oreja, y en el caso de aplicación descrito aquí están conectados mediante puntas de prueba con resorte (GKS) de INGUN. Estos componentes, llamados puntas de prueba con resorte de carrera corta, están realizados de forma muy compacta, y aseguran la transmisión eléctrica (40 mA a 6 V) de la batería al procesador de audio, así como el rápido cambio de los grupos de componentes.
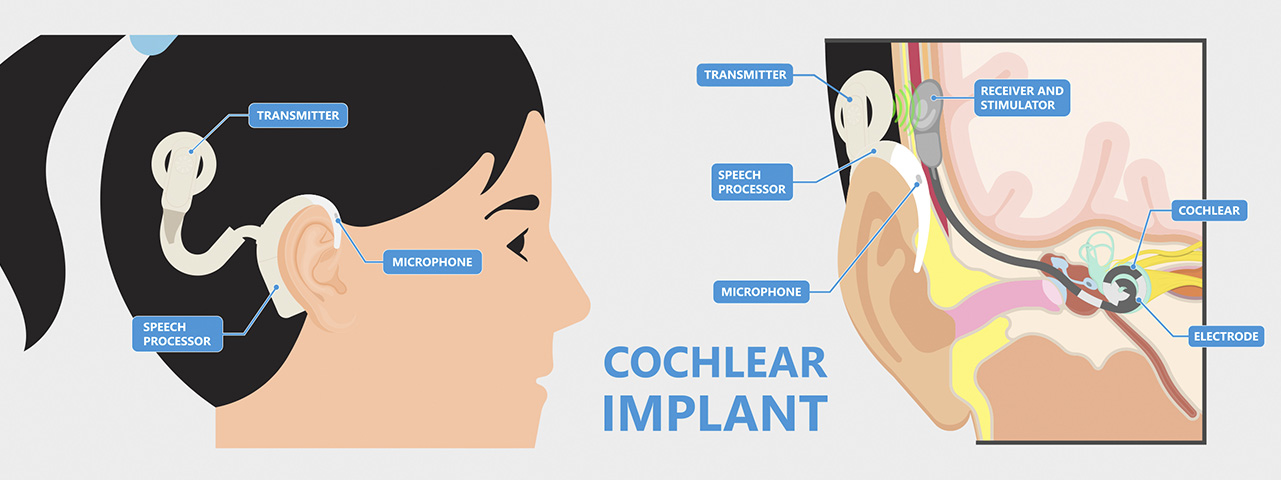
Aunque las puntas de prueba cuentan con un acabado adecuado, y ya habían sido probadas antes con sudor artificial, en la práctica resultó que las exigencias a la resistencia contra la corrosión son extraordinarias en una aplicación de este tipo. La combinación de diferentes metales (soldadura y acabado), sudor y residuos corporales como electrolitos, así como el flujo de corriente eléctrica, da como resultado un elemento galvánico que ocasiona una corrosión electroquímica potenciada, hasta llegar incluso a perder la función: Los pistones se traban en cuanto el resorte montado se ve atacado de manera muy intensa. En el análisis de las impurezas se mostraron, además de los diferentes componentes metálicos, como estaño, zinc, cobre, oro y níquel, también sodio, cloro, carbono y oxígeno, que provienen de residuos del cuerpo.
Como respuesta a este desafío, INGUN realizó una prueba ampliada de corrosión, en coordinación con el cliente, un fabricante de IC, y en colaboración con la Escuela Técnica de Constanza. Por un lado, el objetivo consistía en determinar lo más exactamente posible la magnitud de la corrosión y sus causas. Para esto se realizó una prueba de acuerdo con DIN 50018 (clima cambiante con condensación de agua con atmósfera que contiene dióxido de azufre) con una carga adicional de cloruro. Por otro lado, se trataba sobre todo de determinar la influencia de la soldadura y los fundentes sobre la magnitud de la corrosión, así como encontrar combinaciones que se mostraran menos susceptibles, y por lo tanto pudieran garantizar una más larga vida útil.
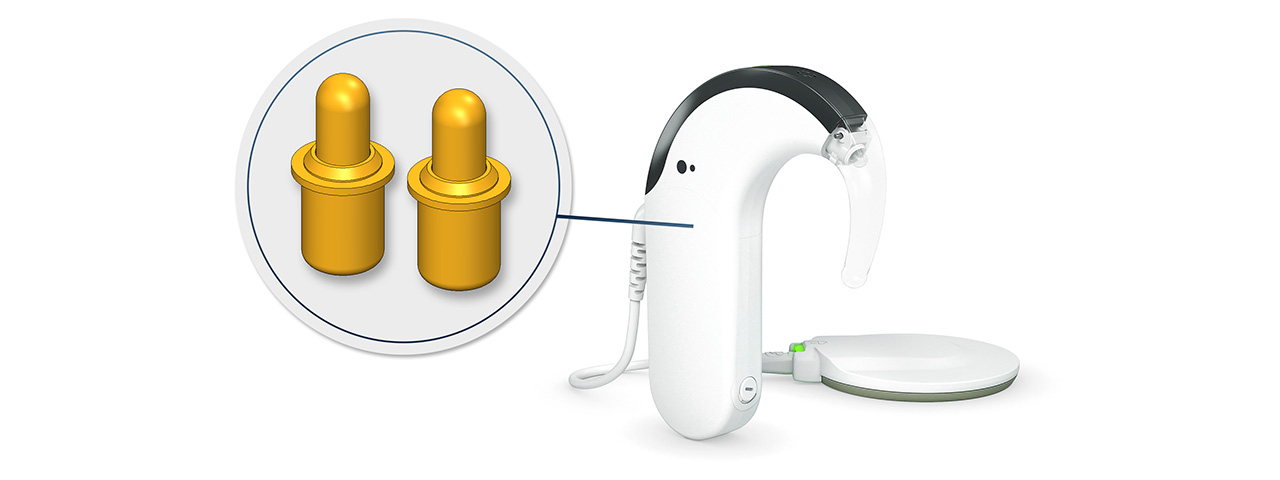
Peter Breul, administrador de proyecto de muestras para prueba (proyectos de diseño) en INGUN, explica el trasfondo: “Aquí tenemos que ver con una complejidad química que no es para subestimarla: Primero, nuestras puntas de prueba están sometidas a una lubricación constante para asegurar el contacto. Después, al realizar el montaje se utilizan diferentes soldaduras, así como un fundente adecuado para alcanzar la capacidad de soldadura. Aquí se trata de alcanzar un grado óptimo entre la agresividad para el grabado con ácido de la placa de circuitos impresos que se utiliza para producir un contacto eléctrico, así como frente a eso una protección adecuada contra la corrosión. Especialmente en las capas exteriores, como en los puntos de soldadura, y la vía, se realizan regularmente aleaciones, que son difíciles de controlar.”
En la prueba de corrosión, las 16 diferentes puntas de prueba en cuatro grupos mostraron en parte resultados muy diferentes, desde fuertemente atacadas hasta solo con impurezas superficiales (y después del baño ultrasónico de nuevo casi “como nuevas”). En los siguientes pasos finalmente se llegó al resultado de que la utilización de una soldadura de plata en combinación con un fundente adecuado reduce claramente la corrosión. Además, un resorte de acero inoxidable en la punta de prueba contribuye decisivamente a mantener el funcionamiento a lo largo de un periodo de tiempo más prolongado. “Otro incremento de la vida útil podría lograrse mediante un acabado optimizado, aunque esto ya no fue considerado por el cliente”, continúa Peter Breul.
Después de utilizar las puntas de prueba con resorte adaptadas adecuadamente, ya no se produjeron averías en una fase temprana con el cliente final: tanto la funcionalidad como las superficies soportaron el entorno fuertemente corrosivo por mucho tiempo. De esta manera, las pruebas de corrosión son un medio eficaz para obtener información confiable en condiciones difíciles de utilización o limpieza sobre la capacidad de las puntas de carga y transferencia. Esto va más allá de la tecnología médica, y en principio afecta a toda el área de los gadgets y wearables. Además de las pruebas de corrosión en sentido estricto, en otras áreas se realizan otros procedimientos, por ejemplo las pruebas de niebla salina o de vibración. Cuando se requiere, INGUN realiza tales pruebas de envejecimiento en coordinación con los clientes, para optimizar el desempeño y la vida útil de las puntas de prueba con resorte y los demás componentes.