TECHNIQUES MÉDICALES
Pour l’être humain, entendre revêt une importance cruciale, notamment comprendre la langue dans le cadre de la communication avec ses semblables. Lorsque les déficiences innées ou acquises de l’ouïe ne se laissent plus corriger avec un amplificateur du son – ce qu’est, techniquement, une prothèse auditive –, il reste encore une autre possibilité : Un implant cochléaire (IC) ainsi nommé stimule le nerf auditif intact à l’aide d’électrodes implantées dans la cochlée (du latin « cochlea »). Le système complet se compose, outre la bobine émettrice (externe) et son homologue réceptrice (interne), également d’un processeur audio avec micro, lequel numérise les signaux acoustiques reçus avant leur transmission vers l’intérieur et provoque des stimulations correspondantes du nerf auditif. La réception vocale ne suit toutefois pas la voie naturelle : la compréhension de ce qui est entendu doit en pratique faire l’objet d’un nouvel entraînement intensif, un peu comparable à l’acquisition d’une langue étrangère.
Tandis que l’alimentation électrique des composants implantés est assurée par induction électromagnétique – les bobines respectivement interne et externe sont maintenues en position réciproque par des aimants –, le processeur vocal externe fonctionne sur batterie. Ces deux modules se portent normalement derrière l’oreille et sont reliés, dans le cas d’application ici décrit, par des pointes de test à ressort (GKS) INGUN. Ces GKS dites à course courte sont réalisées très compactes et assurent la transmission électrique (40 mA sous 6 V) de la batterie vers le processeur audio, ainsi que le remplacement rapide des modules.
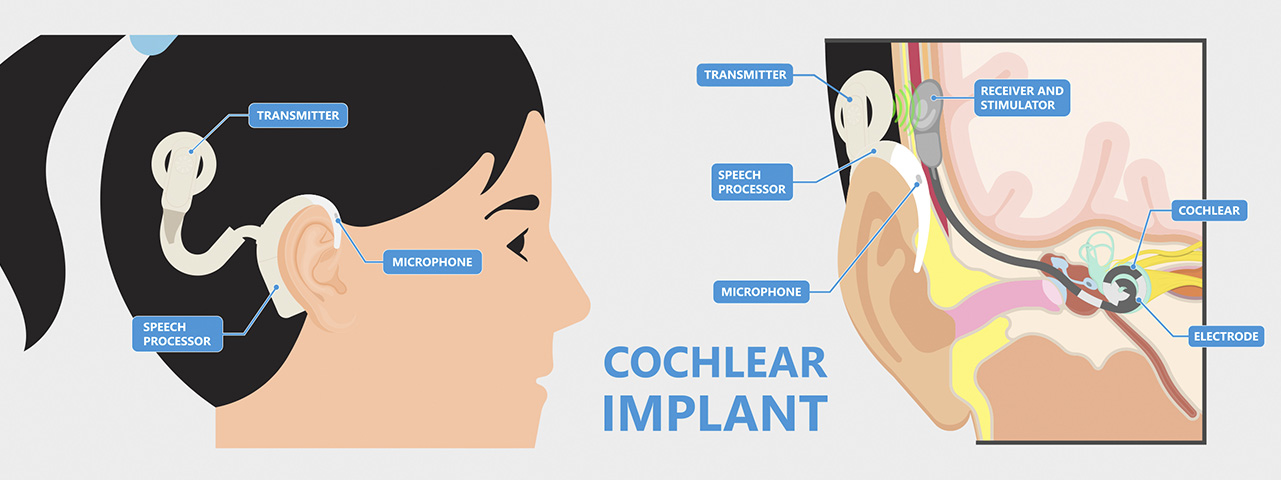
Bien que les pointes de test présentent une finition correspondante et qu’elles aient été testées au préalable avec de la sueur artificielle, il s’est avéré dans la pratique que les exigences visant la résistance à la corrosion étaient inhabituellement élevées dans une telle application. La combinaison de différents métaux (d’apport et de finition), la sueur et des résidus corporels officiant d’électrolyte plus la circulation du courant électrique créent un élément galvanique conduisant à une corrosion électrochimique accrue, voire à un dysfonctionnement : les pistons se coincent dès que le ressort intégré est trop fortement attaqué. L’analyse des impuretés a fait apparaître, outre les différents métaux employés (étain, zinc, cuivre, or et nickel), également d’autres substances, à savoir du sodium, chlore, carbone et de l’oxygène en provenance de résidus corporels.
En réponse à ce défi et en concertation avec le client, un fabricant d’IC, INGUN, en collaboration avec la haute-école technique de Constance, a accompli un test de corrosion élargi. L’objectif a consisté d’une part à déterminer l’ampleur de la corrosion et ses causes avec un maximum de précision. À cette fin, un test selon DIN 50018 (climat alterné avec eau condensée et atmosphère chargée de dioxyde de soufre) avec ajout d’une pollution au chlore a été réalisé. Il s’agissait d’autre part surtout de déterminer l’influence du métal d’apport et du fondant sur l’ampleur de la corrosion, ainsi que de trouver des combinaisons moins vulnérables et susceptibles ainsi d’assurer des durées de vie plus longues.
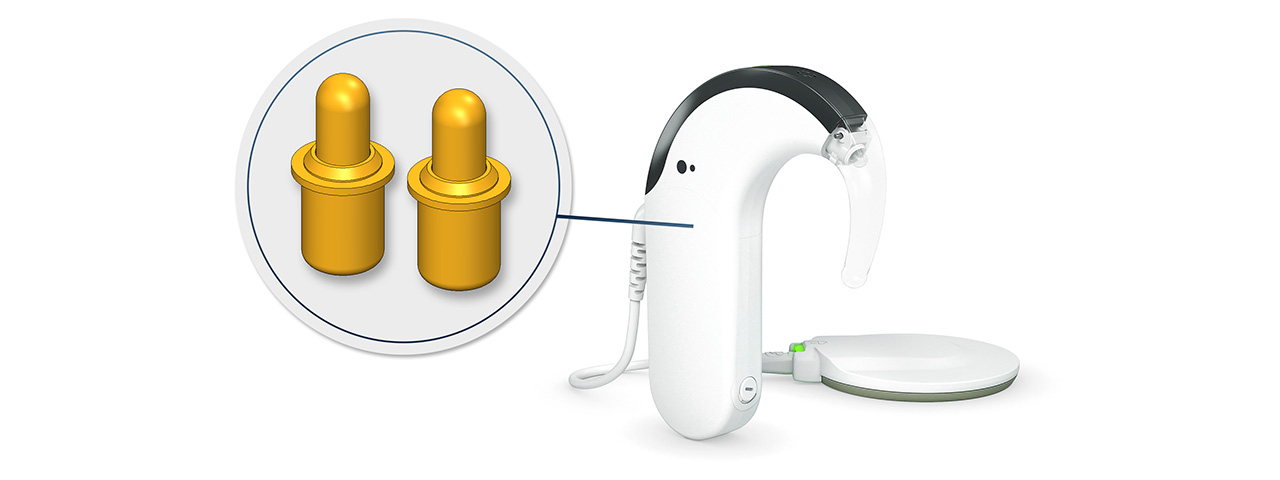
Peter Breul, Test Probe Project Administrator (Design Projects) chez INGUN, explique le contexte : « Nous sommes ici face à une complexité chimique qu’il faut se garder de sous-estimer : dans un premier temps nos pointes de test sont soumises à une lubrification permanente pour assurer le maintien du contact. Ensuite, lors de l’incorporation, différents alliages d’apport et un fondant approprié sont mis en œuvre pour obtenir la soudabilité. Il s’agit ici de trouver un compromis optimal entre l’agressivité requise pour graver chimiquement la carte servant à établir un contact électrique et, en face, une protection anticorrosion suffisante. En particulier sur les couches marginales telles que le point de soudure et le Via se forment régulièrement des alliages difficiles à contrôler. »
Lors de l’essai de corrosion, les 16 pointes de test différentes réparties en quatre groupes ont donné des résultats très différents pour certaines, les unes très fortement attaquées, les autres ne présentant que des impuretés superficielles (redevenues « presque neuves » après le bain ultrasonique). Au cours d’étapes supplémentaires, il est apparu enfin que l’utilisation d’un alliage argentique combiné avec un fondant adéquat réduisait nettement la corrosion. Par ailleurs, un ressort en acier inoxydable dans la pointe de test contribue décisivement au maintien de la fonction sur une période prolongée. « Une augmentation supplémentaire de la durée de vie pourrait être obtenue via une finition optimisée, ce que le client n’a toutefois pas considéré plus avant », poursuit Peter Breul.
Après la mise en œuvre des GKS adaptées de la sorte, il n’y a plus eu de défaillances prématurées chez les clients en fin de chaîne : aussi bien la fonctionnalité que les surfaces ont résisté pendant une durée prolongée à leur environnement très corrosif. Les tests anticorrosion sont donc un moyen efficace pour obtenir, dans des conditions de mise en œuvre et de nettoyage difficiles, des informations fiables quant à la performance des pointes de recharge et de celles de transmission. Cela dépasse aussi le domaine des techniques médicales et concerne en principe l’ensemble du domaine des gadgets et objets portables. Outre les tests de corrosion au sens strict, d’autres secteurs recourent à des procédés supplémentaires dont par exemple des tests au brouillard salin ou tests vibratoires. En concertation avec des clients, INGUN réalise de tels tests de vieillissement suivant besoin pour optimiser la performance et la durée de vie des GKS et d’autres composants.