FORMATION DES CELLULES DE BATTERIE
Dans la troisième et dernière phase de fabrication d’une batterie lithium-ions, l’étape dite de formation est décisive. Après que tous les composants ont été fabriqués, assemblés et emballés, la batterie est une première fois chargée et déchargée de manière contrôlée. Au cours de cette opération, il se forme une couche limite entre l’anode et l’électrolyte, due à l’augmentation successive des intensités ; il s’agit de la couche dite SEI (Solid Electrolyte Interphase).
Ce processus peut durer jusqu’à 24 heures et est déterminant aussi bien pour la qualité électrochimique que pour la performance de la batterie. Les fabricants de cellules investissent par conséquent des ressources considérables pour optimiser le processus de formation, en particulier dans les grandes batteries automobiles requérant des intensités élevées.
Mise en contact énergétiquement efficace pour les hautes intensités
Le choix des solutions de mise en contact joue un rôle capital dans la consommation de courant et dans le développement de la température pendant le processus de formation. La résistance entre l’élément de contact et les pôles de la batterie constitue le plus important facteur de perte. Les alliages en aluminium des pôles des batteries tendent à former une couche d’oxyde qui gêne la circulation des électrons et génère de la chaleur supplémentaire, deux facteurs qui ralentissent le processus de formation. Pour raccourcir le temps de formation et abaisser la consommation d’énergie, il faut maintenir la résistance du contact aussi faible que possible.
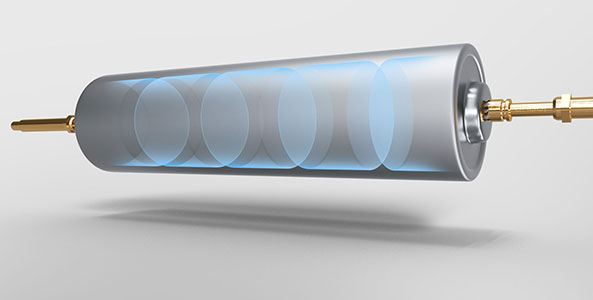
Moins de résistance, moins de pertes thermiques
INGUN propose des solutions de mise en contact innovantes, qui minimisent la résistance des contacts grâce à des formes de tête spéciales et des forces d’applique importantes, ce qui permet des intensités plus élevées et des cycles de charge et décharge plus rapides. Cela accélère le processus de formation et réduit les frais d’exploitation.
Les séries BCP (Battery Contact Probe) et BCC (Battery Contact Clamp) offrent des conditions préalables optimales pour une formation des batteries efficace et économe en énergie.
En voici les principales caractéristiques :
- Alliage de haute qualité : Un revêtement spécial empêche l’oxydation et garantit des connexions longue durée et fiables.
- Câble immobile : Le montage direct sur des barres électriques dispense de montages coûteux de câbles, pour une stabilité maximale et une installation simplifiée.
- Forme de tête unique en son genre : Les pointes de contact traversent sans effort les couches d’oxyde d’aluminium et veillent ainsi à une mise en contact sûre et à perte réduite.
- Options de refroidissement flexibles : Des dispositifs de refroidissement aussi bien actifs que passifs sont disponibles et adaptés de façon optimale aux exigences du processus de formation.
Évoluer et équiper de manière flexible
Le potentiel d’économies continue de s’accroître si plusieurs pointes de contact sont connectées en parallèle, par exemple pour mettre en contact de grandes batteries au niveau du module ou du pack. À cette fin, nous avons développé la pointe Multihead : Cette technologie permet de combiner en souplesse différentes pointes de contact présentant des formes de têtes, forces de ressorts et revêtements différents. Il est également possible, suivant besoin, d’intégrer des dispositifs voltmétriques et thermométriques ainsi qu’un refroidissement actif pour optimiser encore plus le processus de formation.
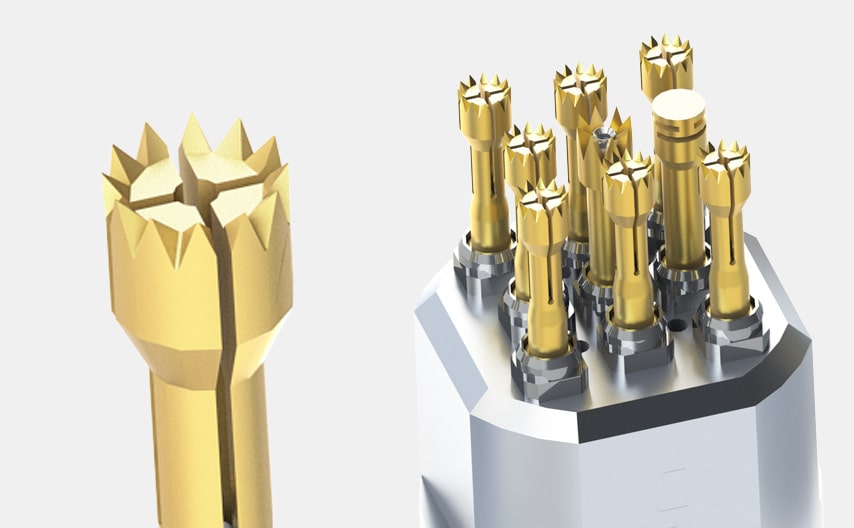