AUTOMATION MADE EASY
Using the automatic opener/closer, manual test fixtures can be retrofitted to boost their performance
For the automation of test processes INGUN offers functional units which can be retrofitted and installed on manual test fixtures and enable automated opening and closing as well as automated contacting of DUTs/PCBs.
To avoid potential risks for the operators, we supply an optional safety switch unit which stops the automatic opener/closer immediately if necessary.
By referring to the reference design document, you can easily realise the control of the electric drive.
- Increased productivity
- Flexible approach
- Optimum safety
- Retrofit kit
Video: Automatic opener/closers for automation of manual test fixtures
Flexible test processes thanks to automation
The automated manual test fixtures can still be used manually, if required, after quick and easy retooling. This ensures maximum flexibility in the test process, depending on the number of DUT/PCB versions and quantities.
Employees are relieved of routine tasks and can focus more skilled tasks.
Benefits at a glance
- Automation of the test process with manual text fixtures already in use
- Increased productivity
- Safe operation thanks to optional safety switch unit
- Easy retrofitting and seamless integration thanks to INGUN's reference design document
- Ergonomic loading of the test fixture by operator or robot/cobot
- Manual operation for inspection, maintenance, or troubleshooting still possible
- Robust, cost-effective electric drive, no pneumatics required
- Long service life - parts subject to wear easily replaceable and readily available
- Comprehensive video and instructions for installation on-site
Increase efficiency and productivity
A growing number of companies are automating manual test processes in production.
Practical automation measures can reduce costs, increase productivity, and reduce errors. Automation is particularly important when the quantities to be produced require safe, reliable operation around the clock. In addition, automation relieves your employees and allows them to take on more skilled, valuable tasks than repeatedly opening, closing, and loading test fixtures.
From the manual testing process to the fully automated production line:
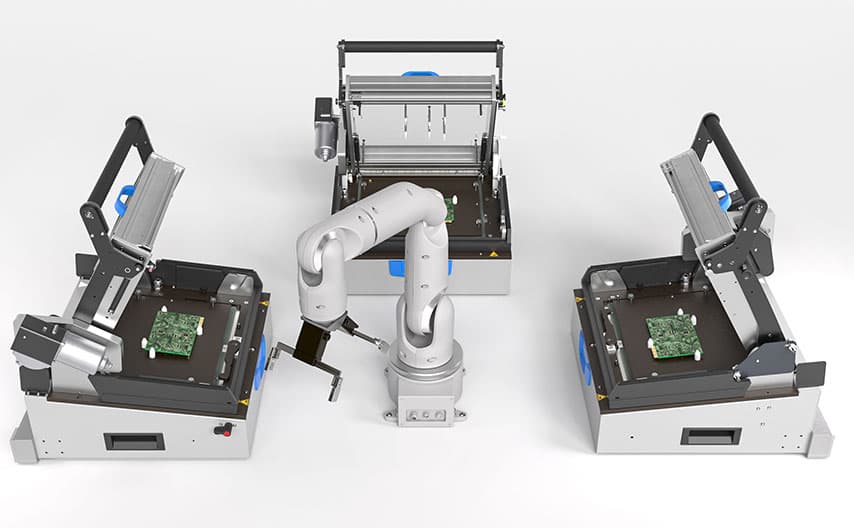
Functionality and key figures
The electric drive used is a geared motor with 12 V DC voltage: it drives the toothed segment of the drive unit's coupling via a gear wheel. The particularly robust design enables a contact force of up to 1000 N and a service life of up to 500,000 load cycles*.
Regardless of whether the test fixture is loaded (insertion and removal of the DUT/PCB) by an operator or robot/cobot, the 70° opening angle of the pressure frame provides sufficient leeway for ergonomic handling.
The simple removal of the cover and a gear wheel according to the instructions makes it possible to continue to operate the test fixture manually for maintenance or troubleshooting.
Retrofitting made easy
The automatic opener/closer functional units have been designed to be retrofitted and installed on manual test fixtures already in use. They are available for all manual test fixtures in the MA2xxx series (except the MA2x13 tandem version).
Optimum safety
Automation also fundamentally results in potential risks that must be minimised using suitable protective devices to ensure the safety of operators. The optionally available safety switch unit has a safety stop function that stops the electric drive if necessary and protects operators from injury. The safety switch unit can be optionally retrofitted and operated using a customer-supplied control system. The use of the safety switch unit is recommended when, for example, automated test fixtures are used in openly accessible or unsecured areas.
Ensuring a good connection – flexible, seamless integration into your test environment
The automatic opener/closers with optional safety switch units can be easily integrated into an existing test environment. In a comprehensive reference design document, we provide information about the requirements for control system connection and operational safety. In addition, we demonstrate how the functional units can be safely implemented in practice using an exemplary configuration that includes all basic functions.
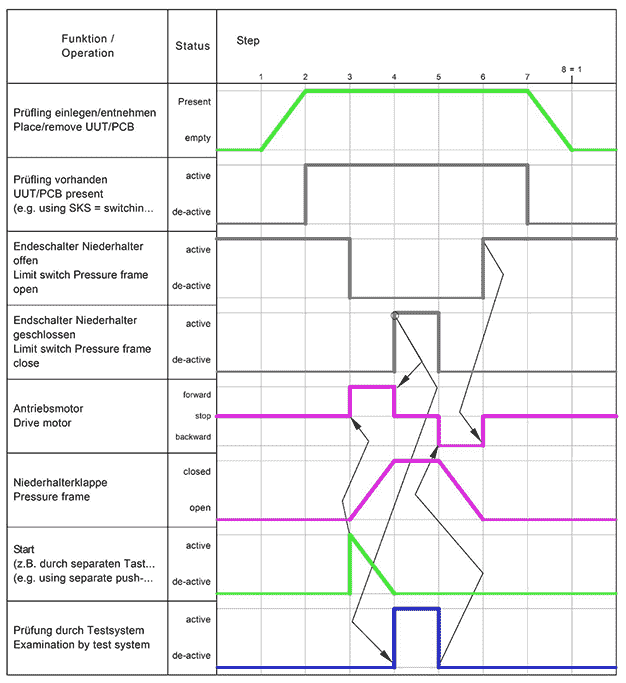