电池单元成型
化成 (Formation) 是锂离子电池制造第三阶段也是最后阶段的决定性步骤:所有组件制造、组装、封装完毕后,电池将首次以受控方式进行充放电。随着电流逐渐增大,阳极和电解质之间会形成边界层,称为 SEI 层(固体电解质界面)。
这一过程可长达 24 小时,对电池的电化学质量和性能至关重要。因此,电池制造商投入大量资源来优化化成工艺,尤其是针对需要大电流的大型车用电池。
适合大电流应用的高能效触探
选择合适的触探解决方案,对化成过程中的功耗和温度曲线至关重要。最大的损耗因素是接触元件与电池电极之间的接触电阻。电池电极的铝合金容易形成氧化层,阻碍电子流动并产生额外热量,这两者都会减慢化成过程。为了缩短成型时间、降低能耗,应尽可能降低接触电阻。
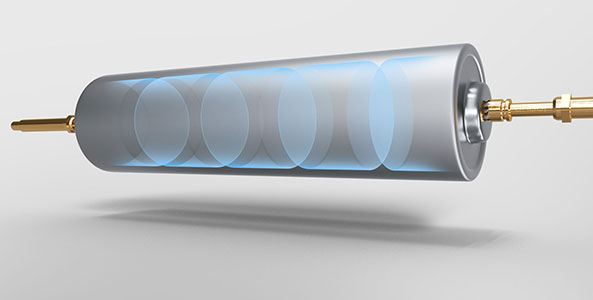
电阻更小,减少热损耗
INGUN 提供创新触探解决方案,凭借特殊针头形状和大压紧力,将接触电阻降至最低,以此实现更大电流和更快的充放电周期,从而加速化成过程、降低运营成本。
BCP 系列(电池触探探针 和 BCC 系列(电池触探夹 可助力实现高效节能的化成工艺。
其具有以下重要特点:
- 优质合金:特殊涂层可防止腐蚀变色,确保连接持久可靠。
- 无活动电缆:直接安装在汇流排上,无需费力安装电缆,可最大限度提高稳定性并简化安装。
- 独特的针头形状:探针能够轻松穿透氧化铝层,确保触探可靠、损耗低。
- 灵活的冷却选项:可提供主动和被动冷却系统,确保满足化成工艺要求。
轻松扩展、灵活装配
若将多根探针并联,例如在模块和电池包层面触探大型电池,则可进一步提高节能潜力。为此,我们开发了 多头 平台:借助这项技术,可将针头形状、弹簧力和涂层各异的多根探针灵活组合。如有需要,还可集成电压和温度测量以及主动冷却功能,从而进一步优化化成工艺。
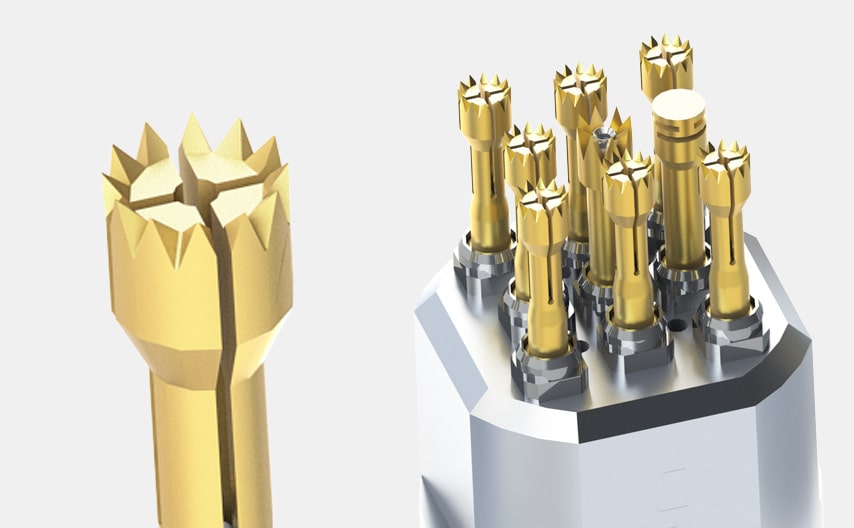